Small nut Big duty
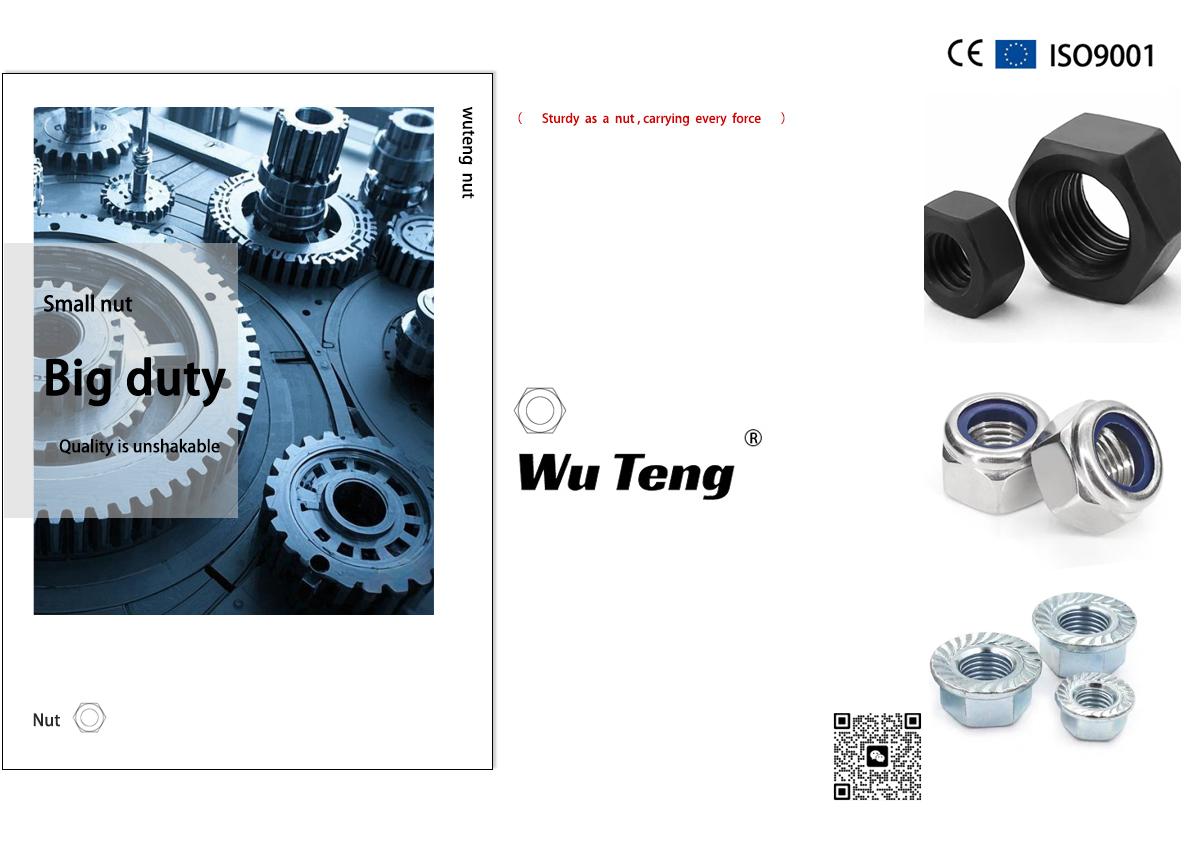
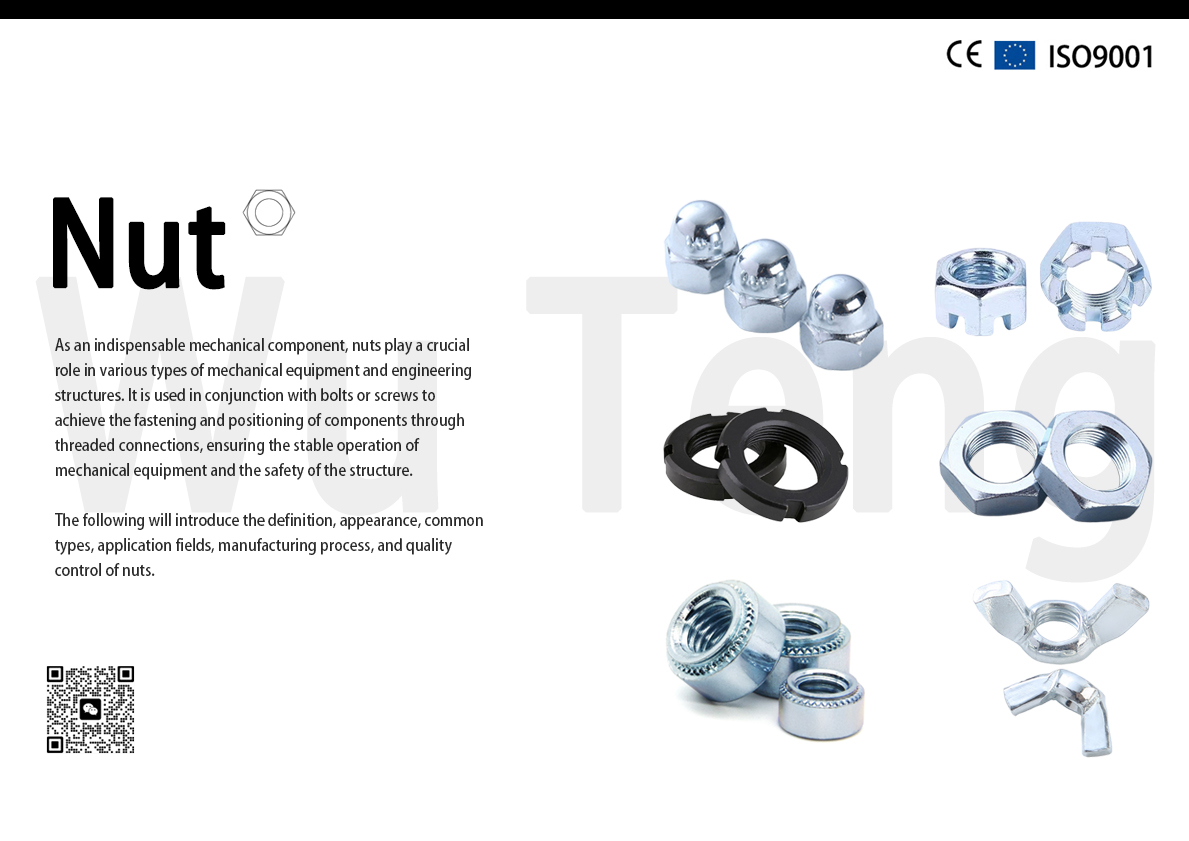
Ⅰ、 Definition and appearance of nuts
A nut is a fastener with internal threads that is used in conjunction with a bolt. Usually hexagonal, circular, or square in shape, with hexagonal nuts being the most common. The hexagonal design facilitates the use of tools such as wrenches for tightening and loosening operations, providing a larger torque application surface to ensure the tightening effect. The nut has a threaded internal thread that matches the specifications and pitch of the corresponding bolt, achieving precise connection.
Ⅱ 、 The types of nuts are very diverse, mainly including the following common types:
1. Outer hexagon nut: This type of nut is hexagonal in shape, making it easy to tighten or loosen with a wrench. According to the nominal thickness, hex nuts are classified as Type I, Type II, and Thin. Type I nuts are divided into Class A, Class B, and Class C. Class A and Class B are suitable for machines and equipment with low surface roughness and high precision requirements, while Class C is used for situations with rough surfaces and low precision requirements. Type II hex nuts are commonly used in situations where disassembly is necessary due to their thicker thickness.
2. Flange face nut: This type of nut has a wide edge at the bottom that resembles a flange edge, with a built-in gasket structure and good anti loosening performance. It is commonly used in conjunction with T-bolts in the automation industry, or when installing profile accessories such as corner pieces.
3. Cap nut: The cap nut comes with a closed lid to protect the threads and prevent loosening. It is commonly used for connecting exterior components of automobiles, exterior parts of mechanical equipment, and connection parts of outdoor facilities.
4. Nylon nut: Made of nylon, it has excellent insulation, non-magnetic, thermal insulation, high temperature resistance, high strength, and corrosion resistance. It is commonly used in the electroplating and communication industries and does not generate signal interference such as eddy currents, making it suitable for use in strong acid-base environments.
5. Slotted Nut: Slotted nuts are used in conjunction with perforated bolts and split pins to prevent relative rotation between bolts and nuts. They are commonly used in situations where precise power transmission is required, such as the bogies of trains and high-speed trains.
6. Butterfly Nut: Butterfly nuts are named after their unique butterfly wing appearance, making them easy to twist by hand and commonly used in small furniture, electrical equipment, toy manufacturing, and other fields.
7. Square Nut: Square nuts are named after their unique square design and are commonly used in applications that require high-strength connections, such as heavy machinery, vehicle manufacturing, and construction industries. Its superior stability and connection strength make it widely used in multiple fields.
8. T-shaped nut: T-shaped nuts are commonly used in the construction of aluminum profile frames for automated production lines, logistics and warehousing equipment, and other occasions.
9. Anti loosening nut: There are various anti loosening designs to prevent loosening under vibration or impact loads. Like a nylon lock nut, insert a nylon ring at one end of the nut to increase friction and prevent loosening; Spring washer nut, utilizing the elastic deformation of the spring washer to provide additional friction force; There is also a slotted nut that is matched with a split pin to lock the nut mechanically.
10. Thin nut: thinner than ordinary nuts, suitable for space limited situations, reducing the weight of connecting components, but with relatively low load-bearing capacity, commonly used for light load connections with low strength requirements.
11. Welding nuts: pre welded onto components for easy bolt assembly, reducing assembly processes and improving production efficiency. They are commonly used in industries such as automotive manufacturing and steel structures.
These nuts have their specific purposes.
Ⅲ 、 Application Fields
1. Mechanical manufacturing: The assembly and debugging of various types of machine tools, engines, cranes, and other mechanical equipment cannot be separated from nuts, which are used to connect different components to ensure equipment accuracy and stability.
2. Automotive industry: From the engine, chassis to the body, nuts are widely used for component connections, with extremely high requirements for the strength and reliability of nuts to ensure safe driving of automobiles.
3. Construction engineering: In steel structure buildings and bridge construction, nuts are used to connect steel beams, steel columns, and other components, bearing huge loads, and are key components to ensure the stability of building structures.
4. Electronic appliances: In electronic products, nuts are used to fix components such as circuit boards and casings. Nut size accuracy and corrosion resistance are required to adapt to the miniaturization and high reliability requirements of electronic devices.
Ⅳ、 Manufacturing process
1. Cold heading forming: Metal wire is forged into the approximate shape of a nut at room temperature using a cold heading machine, which is highly efficient and material efficient, and suitable for mass production of standard specification nuts.
2. Hot forging forming: For some large or high-strength nuts, hot forging technology is used to forge the heated metal blank in the mold, improve the metal structure and properties, and enhance the nut strength.
3. Thread processing: The formed nut blank needs to be threaded, and common methods include cutting (such as turning, tapping) and rolling. Rolling thread has high efficiency, good surface quality, high thread strength, and is widely used.
4. Surface treatment: To improve the corrosion resistance and aesthetics of the nut, surface treatments such as galvanizing, nickel plating, and blackening are carried out, and the appropriate treatment method is selected according to the usage environment.
Ⅴ、 Quality control
1. Dimensional accuracy testing: Use measuring tools (such as calipers, thread plug gauges, etc.) to strictly measure the outer diameter, inner diameter, thickness, pitch, and other dimensions of the nut to ensure compliance with standard tolerance requirements.
2. Material inspection: The nut material is inspected through chemical analysis, hardness testing, metallographic analysis, and other methods to ensure that its chemical composition and mechanical properties meet the design requirements.
3. Appearance inspection: Check the surface quality of the nut manually or with the help of a machine vision system, and do not allow defects such as cracks, sand holes, pores, slag inclusions, etc.
4. Torque testing: Simulate actual usage conditions, conduct torque testing on nuts, inspect their tightening and loosening performance, and ensure normal operation within the specified torque range.
Nuts may seem simple, but they play an irreplaceable role in modern industry and daily life. With the development of technology and industrial progress, the design, manufacturing process, and quality control of nuts will continue to improve to meet the growing demands of various industries and provide solid guarantees for the safe and stable operation of various complex engineering and mechanical equipment.
Post time: 3月-19-2025